You are taking the right step in the right direction
Our pricing adapts to your size. Whether you’re a large industrial company or a small
manufacturing plant looking to improve your efficiency, we can help you out.
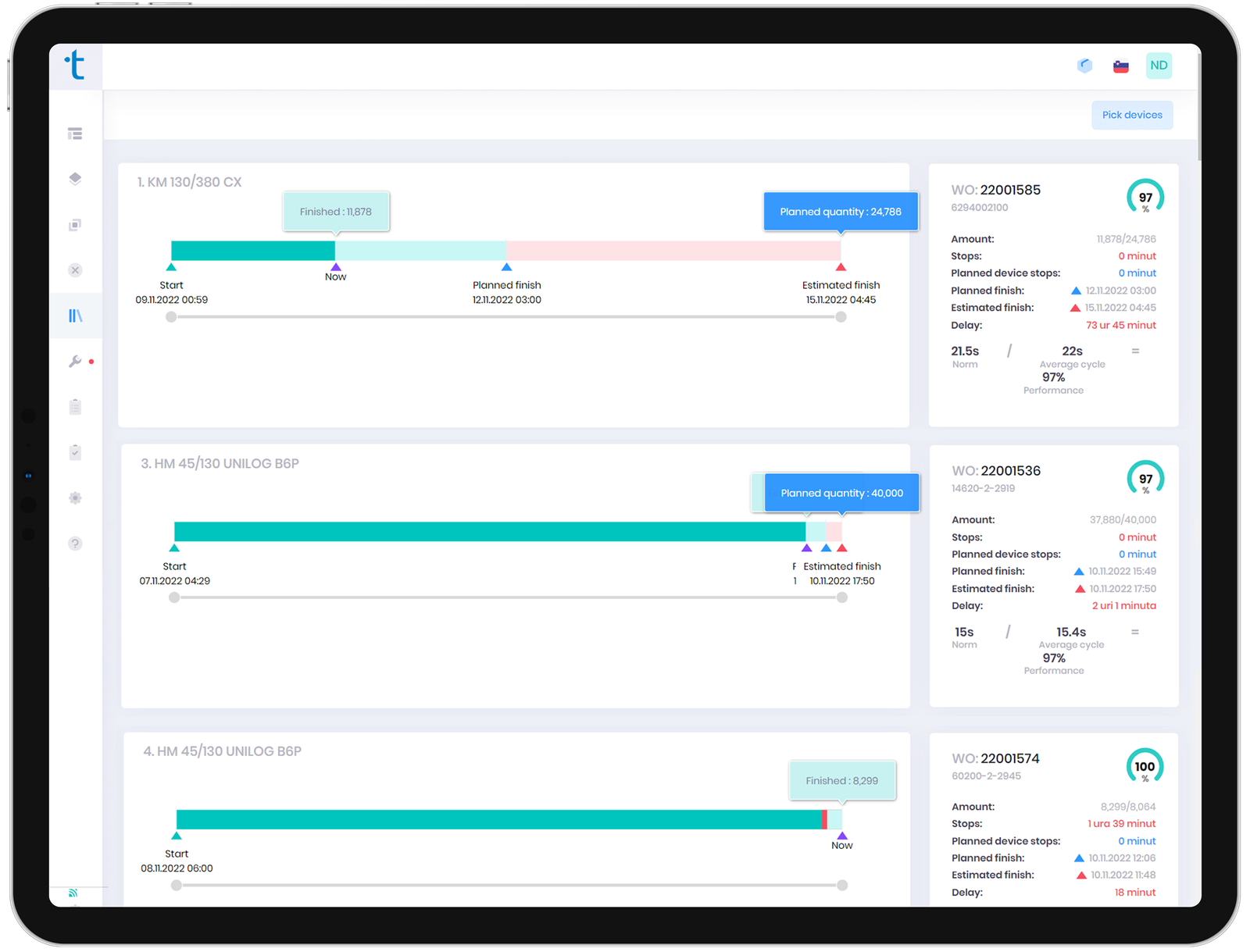
Get A Quote
Frequently Asked Questions
Tipteh is the concept of a modern facility equipped with cutting-edge technology in favor of production optimization and higher efficiency. Tipteh philosophy fits in the current trends of the Internet of Things, Industry 4.0, and lean manufacturing.
Tipteh is a general name for the entire Tipteh software ecosystem. Tipteh consists of 4 in-app products and addons which are tailored to customers’ needs and requirements. Regardless of the customer’s custom configuration, the goal is to make your factory modern and smart!
Yes, Tipteh’s team proposes the most suitable hardware for the given project. As an end-to-end company, we configure, deliver and install all necessary wiring and appliances along with our software.
Tipteh solutions provide our customers with the platform in a private, public, or hybrid cloud architecture. Legacy on-premises solutions are also available if the project demands domestic infrastructure due to its specification.
No, a Tipteh MES (Manufacturing Execution Software) system is not an ERP (Enterprise Resource Planning) system. However, Tipteh provides a system with built-in ERP capabilities if local ERP is not available.
Yes, Tipteh integrates with most systems available on the market (SAP, etc.)
Yes, our experts are ready to share their experience and knowledge with you. After years of putting systems in place, we have developed best practices and protocols to support our clients.
Tipteh supplies an 80% ready-to-work system. 20% is customizable to the customer’s case.
Our dedicated team is ready to connect with old and new machines on the production line. If PLC drivers are not available, we can duplicate the analog signal to get a digital output.
No, ERP is not obligatory to install one of Tipteh’s suites. Our systems have a simplified ERP system already installed.
In order to start the digitalization journey, Tipteh experts have to visit your factory, perform a production health check to discuss business goals and create a solution concept. The whole journey starts with an initial online meeting where we discuss the system, current situation, and the next steps.
Usually, it takes up to 6 months to implement the system and see the first positive results.
Tipteh provides a customer success manager who will help your company prior to and after roll-out by prioritizing issues, controlling tasks, and streamlining the communication between companies. Our experts train you on how to use your system to optimize production. We coach and consult to guide you with the best practices from other industries.
Tipteh’s implementation team visits your factory to implement the solution and ensure that all standards are met, and settings are set up correctly prior to system startup.
Yes, Tipteh is part of the industry 4.0 movement. We deliver our hardware and software according to the newest standards and practices of Industry 4.0.
Of course, we are pleased to invite you to one of our reference sites to show you how the system performs.
The operator uses an access RFID card or pin pad to enter the system on the shop floor.
Tipteh provides 3 suites and additional add-ons which can be modified according to customers’ requirements and factory state.
Yes, if the project requires only a specific functionality to be covered, we will provide one module which can be expanded in the future.
Compare Products
Blog Posts
10 Examples Of Green Manufacturing Practices
April 10, 2023
The aim of this article is to help you become greener. Even some of the big business leaders are leaning to it, like Bill Gates. What Are the 10 Simple...
Read More
Calculating OEE – Formulas & Examples
December 15, 2022
The blog aims to show you how to calculate OEE and its components properly, using formulas and calculation examples. The three formulas that we are going to examine are:1. Availability...
Read More
How does improvement in OEE improve your manufacturing KPI
December 15, 2022
Manufacturers usually monitor several key performance indicators (KPIs) across the plant to see how various functions are performing a particular process. In manufacturing facilities, these parameters are usually shown on...
Read More
The Biggest Mistakes in OEE Calculation and Monitoring
December 15, 2022
OEE has been an effective way to track overall equipment performance for 30 years. However, it is simple to make mistakes in OEE calculation, and given how much they reduce...
Read More
How Waste is Defined in Manufacturing
December 15, 2022
Experts in sustainability, quality assurance, and continuous improvement frequently use the phrase "waste." In every use case, the intention is to attempt and eradicate it, but what exactly should be...
Read More
Merging OEE Monitoring and ISO 50001
December 15, 2022
Energy and manufacturing efficiency both aid businesses in being more environmentally friendly. We explain how ISO 50001 operates in this post, along with the benefits of combining your energy usage...
Read More
Lean Continuous Improvement – Key to Success in Any Industry
December 15, 2022
The extent to which lean continuous improvement (LCI) has impacted how manufacturers conduct business highlights the significance of LCI. The iterative process for achieving incremental gains exemplifies the mindset that...
Read More
Improve your OEE: Switch From Reactive to Predictive Maintenance
December 15, 2022
The day-to-day operations of firms are changing as a result of technology. Major corporations are putting more effort into enhancing product quality, automating procedures at lower costs, and streamlining equipment...
Read More